Automatic production lines save a lot of time and cost. In industrially developed cities, the maintenance of automatic production lines has become a hot spot. Automatic production line maintenance is mainly completed by operators and maintenance workers. Two major methods of automatic production line maintenance: synchronous repair method: in production, if a fault is found, try not to repair it, and take the maintenance method. Make the production line continue production until the holidays, and concentrate maintenance workers and operators to repair all problems at the same time. The equipment was in full-line production as normal on Monday. Partial repair method: If there is a big problem in the automatic production line, the repair time is more frequent. Simultaneous repair method cannot be used. At this time, use the holidays to concentrate maintenance workers and operators to repair a certain part. Wait until next holiday to fix the other part. Ensure that the automatic production line does not stop production during working hours. In addition, try to use the pre-training method in management. Install a timer in the equipment, record the working time of the equipment, apply the wear law to predict the wear of the wearing parts, and replace the wearing parts in advance to eliminate the fault in advance. Ensure that the production line is at full capacity.
Maintenance of automatic production lines: electric circuits, gas circuits, oil circuits and mechanical transmission parts (such as guide rails, etc.) should be inspected and cleaned before and after work; inspections should be conducted during the work process, and key parts should be sampled. Any abnormality should be recorded. After-shift processing (not long), prepare spare parts for major problems; unify the entire line for maintenance, make a plan for wearing parts, and replace wearing parts in advance to prevent problems before they burn. The production line uses the continuous or intermittent motion of the conveyor belt to transport various items of different sizes and weights, which can not only transport various bulk materials, but also various boxes, packaging bags, etc. The production line conveys smoothly, and there is no relative movement between the material and the conveyor belt, which can avoid damage to the conveyed material. Low noise, suitable for occasions where the working environment is relatively quiet. Simple structure and easy maintenance. Low energy consumption and low cost of use. The material of the conveyor belt of the production line includes rubber, rubber and plastic, PVC, PU and other materials. It can not only be used for the transportation of ordinary materials, but also can meet the transportation of materials with special requirements such as oil resistance, corrosion resistance and anti-static.
Geartech Company has long been committed to the research and development, manufacturing and sales of hot-dip galvanized steel production line, color-coated steel plate production line, color-coated aluminum plate production line and aluminum-plastic composite board production line. After years of practical experience and the requirements of customers around the world, it has developed into a professional equipment supplier in the industry. Because of its professionalism, Geartech products are well received by the same industry and users. Geartech is convinced that only professional people do professional things with professional hearts, can we maintain long-term and good common interests of you and me.
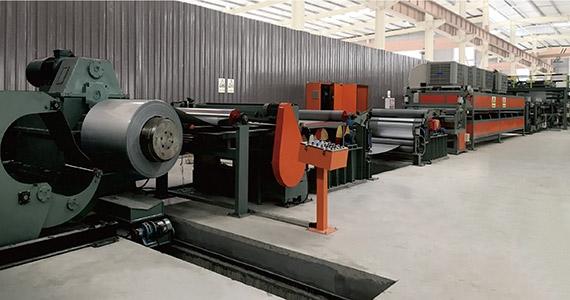