Aluminum Composite Panel Production Coil Coating Lines Manufacturer
Setting up an Aluminum Composite Panel Production Line requires careful planning, the right machinery, and a clear understanding of the manufacturing process. Aluminum composite panels (ACPs) are widely used in the construction, signage, and interior design industries due to their durability, versatility, and aesthetic appeal. To successfully establish a production line, it is essential to focus on several key components that ensure a smooth and efficient operation.
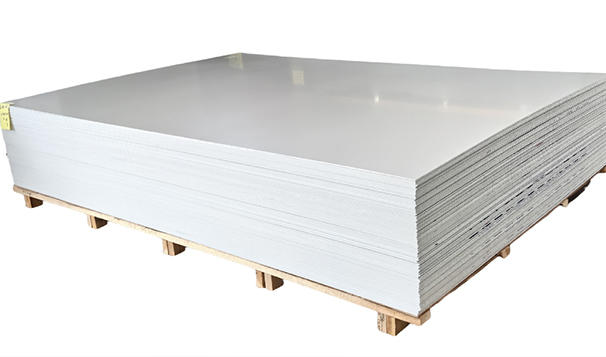
The one step in setting up an Aluminum Composite Panel Production Line is selecting the right materials. ACPs are typically made from two thin layers of aluminum enclosing a non-aluminum core, which can be either a polyethylene or a mineral-based core material. These core materials significantly affect the quality and performance of the final product. It’s crucial to source high-quality aluminum sheets and core materials to ensure the final panels are durable and meet industry standards.
Once the materials are chosen, the next step is to focus on the machinery required for the Aluminum Composite Panel Production Line. The production line typically includes several stages, starting with material preparation and followed by processes such as coating, lamination, and cutting. Each machine within the line must be designed to handle the specific needs of ACP production, ensuring that the final product has the desired thickness, finish, and mechanical properties.
One of the core components of any Aluminum Composite Panel Production Line is the coating machine. This machine applies a protective layer to the aluminum surface, often using a polyester or PVDF coating to enhance resistance to weathering, corrosion, and UV degradation. The coating process also ensures that the surface of the ACP has an aesthetically pleasing finish, which is essential for applications where appearance matters.
The next important part of the Aluminum Composite Panel Production Line is the lamination process. This stage involves bonding the aluminum sheets to the core material using heat and pressure. The lamination process must be carefully controlled to ensure uniform bonding and prevent delamination or other defects that could affect the panel's performance. A specialized lamination press ensures that the layers are securely fused together while maintaining the desired thickness and flatness of the final panel.
After lamination, the Aluminum Composite Panel Production Line moves to the cutting and shaping stages. The panels are typically cut to the required dimensions using a precision cutting machine. The cutting process must be highly accurate to ensure that each panel meets the customer’s specifications and fits the intended application. In some cases, additional shaping processes like edge trimming, perforating, or bending may be required, depending on the design needs of the final product.
Quality control is a critical aspect of the Aluminum Composite Panel Production Line. Throughout the production process, it’s important to monitor the quality of the panels to ensure they meet both internal standards and regulatory requirements. This can be done through visual inspections, thickness measurements, adhesion tests, and other quality assurance techniques. The inspection process ensures that any defects or issues are identified early, preventing defective panels from reaching the market.
To maintain high production efficiency and reduce operational costs, the Aluminum Composite Panel Production Line should also incorporate automation and advanced control systems. These systems can monitor the production process in real time, adjusting settings and parameters as needed to maintain consistent product quality. Automation can also help less human error, speed up production times, and reduce waste, ultimately making the production line more cost-effective.
In addition to the machinery and quality control systems, it’s important to ensure that the Aluminum Composite Panel Production Line is designed for energy efficiency and environmental sustainability. The production of ACPs can be energy-intensive, so selecting energy-efficient equipment and implementing waste-reducing practices can help less the environmental impact of the operation. Recycling scrap materials, using eco-friendly coatings, and optimizing energy use in heating and cooling systems are all ways to reduce the environmental footprint of the production line.
Finally, the setup of an Aluminum Composite Panel Production Line requires skilled personnel who are trained in the operation and maintenance of the machinery. Proper training ensures that workers can handle the equipment safely, troubleshoot issues, and optimize the production process. Regular maintenance of the machinery is also critical to less downtime and keep the production line running smoothly.
In conclusion, setting up an Aluminum Composite Panel Production Line is a complex but rewarding process. It involves selecting high-quality materials, investing in the right machinery, ensuring proper quality control, and optimizing energy efficiency. With the right equipment, skilled personnel, and careful planning, businesses can establish a highly efficient production line that produces high-quality aluminum composite panels to meet market demands. The success of an Aluminum Composite Panel Production Line ultimately depends on the ability to manage each step of the process effectively while maintaining a focus on quality, efficiency, and sustainability.