Coil coating is a highly efficient, automated process that can produce uniform coatings over metal. Today, an estimated 80 percent of metal is painted by coil coating.
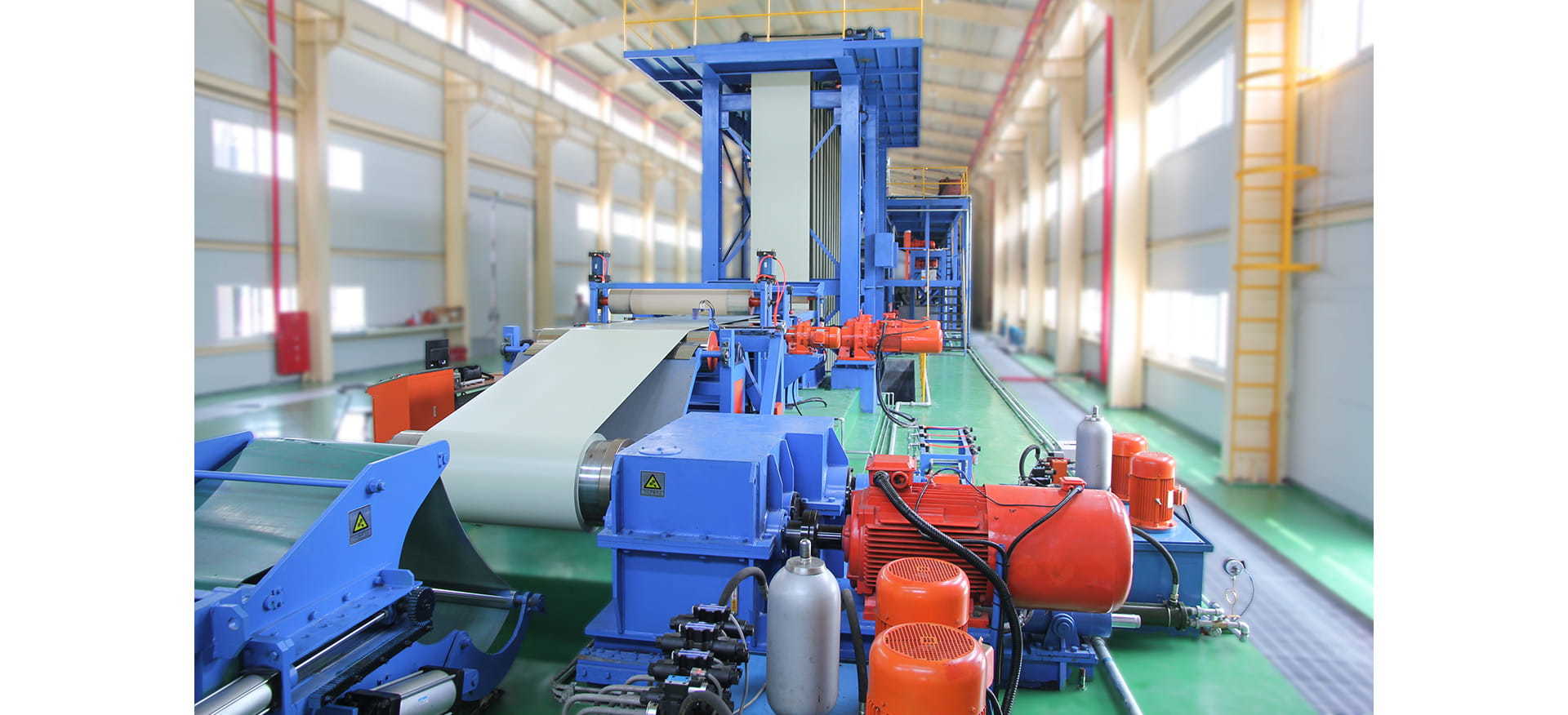
A typical coil coating line consists of decoilers, entry strip accumulator, cleaning, chemical pretreatment, primer coat application, curing, exit accumulator and recoilers. Available coatings include polyesters, plastisols, polyurethanes, PVDF, epoxies, primers, backing coats and laminate films.
The Coil
A coil coating line (CCL) is a type of continuous process that applies specialty coatings to steel and aluminum coils before fabricating into finished products. It is the most popular method for producing high-tech, complex metal coatings, including cool metal roofing materials, smog-eating building panels, antimicrobial products, and solar panels.
The process begins by shearing the coil ends of steel from the cold rolling mill and sending it through one of two payoff reels. The coils are then pushed through an uncoiler, a line-loading accumulator, processed and painted according to requirements, brought through a finish line exit accumulator and rewound on a recoiler.
The coils are then rewound and processed on a second strip accumulator to form a continuous strip of material in the line. This strip is then spliced together in a continuous manner without stopping the line, which allows an unbroken web of metal to be formed with virtually unlimited length.
Pre-treatment
In the coil coating line, pre-treatment is necessary for preparing the steel strip for painting. This pre-treatment helps remove dirt, debris and oils from the metal strip.
Often, it also improves corrosion resistance and surface texture for improved paint adhesion. Depending on the requirements, this process can include a chemical coater and/or a chrome free treatment.
The pre-treatment process for the coil coating line is a very important step that helps ensure long lasting, durable products. It can help dissipate stress under load, improve durability and facilitate consistent and stable distribution of anti-corrosive additives.
The chemistry used for the pre-treatment stage can be very complex and requires a high degree of expertise. AD CCT offers a range of metal surface pre-treatment chemicals designed to meet the needs of different manufacturers and product applications. These chemicals are based on chromates and modern, chrome-free chemistry. These no-rinse processes are eco-friendly as they do not require a significant amount of chromium-bearing wastewater.
Painting
Coil coating is an efficient way to produce a uniform, high quality, coated finish over metal in a continuous automated fashion. Today, over 800 million tons of coil-coated steel are produced and shipped annually.
To achieve this, the steel goes through a series of fully automated production steps that can run continuously (see Diagram I). Compared to other painting methods, it offers nearly 100% utilization of paint during application and is less environmentally damaging.
The process starts when the cold-rolled strip is first unwound, cleaned and pre-treated. The strip then goes through a number of different coating processes to apply one or more layers of paint on a flat continuous sheet, heat cured and cooled before being rewound for shipment.
During the curing section, the strip is passed through a number of ovens to remove solvents and ensure that the paint is fully cured. The curing ovens also recycle 90 percent of the painted coil’s volatile organic compounds (VOCs) back into the line’s fuel system, making it an energy-efficient way to paint metal.
Packaging
Steel coil is the most common form of metal used for roofing, building panels and other products. It's a strong, durable and reliable material that opens up design flexibility and reduces costs.
The cold rolled raw metal that's delivered to our steel mills is tension-leveled before being cut, shaped and rolled into coil. This process prevents the metal from bending and other defects that could affect its finish when it gets to our paint line.
The metal coil is then unwound, cleaned, chemically treated, primers, backers and top coats are applied. It is then rewound and packaged to be shipped to customers.