Choosing the right aluminum coil rewinding machine is not just about the price, but about the features and functionality as well. It is also important to think about the winding head, the speed, and the position of the wire.
During the winding process, unevennesses and bends are commonly incurred during the process. A number of factors contribute to the formation of these wrinkles. One of these is the wire guiding nozzle. This is an important component in the process.
The winding process involves the use of a guiding tube, which is designed to distribute the wire throughout the body of the coil. This will help to minimise the volume of materials and reduce the amount of space required for insulation between layers.
Winding a coil is a cyclic process that involves the movement of the work roll and the wire. When winding the wire, it is important to enter the winding area in a flat angle. This ensures that there is no unnecessary bending of the wire. A flat angle is also an effective way to minimise the amount of space needed for the second winding step.
During the process of making a coil, two factors influence its performance: the winding method and the raw materials used. The winding method is determined by the wire gauge, the number of turns, the shape of the form, and the spacing between turns. The raw materials used determine the strength and inductance of the coil.
The winding process begins with the wire being fed from a feed wire shaft. The wire is then guided into the winding area, as evenly as possible. The last guided point of the wire must be at the nozzle. The wire parking pin must be cut or clamped before the winding process begins.
Creating the entire stator with a single tooth chain is complex. To achieve this, the multi-layered winding technique is used. Using this method, several conductors are layered one over the other and the entire winding is insulated with insulation paper.
For the best packing of round wires, the wires in the upper layer should be in grooves of the lower layer for at least 300 degrees of the coil circumference. This allows the fill factor to increase, which results in higher conductivity and efficiency.
The multi-layered winding device is helpful in cases of low voltage and high current. In this method, spacers are placed between adjacent turns to maintain the spacing.
Creating a certain winding head shape allows a rotor to be installed
During winding, the wire guiding nozzle has a wide range of possible movements. Some can be very smooth while others are more gradual. It can be controlled by three CNC axes.
The wire guiding nozzle can also be controlled by a coil body post. This is especially helpful when the wire is being wound on heavy metal sheets.
It is also possible to use cut-and-clamp contacts for plugged tooth coils. These are usually used in the outer part of the back of the tooth. The purpose of this slot is to provide a way for the tooth to be securely mounted in the winding device.
Another type of slot is a teardrop-shaped slot. These types of slots are useful because they help with capacity and minimize the impact on magnetic flux.
During the process of rewinding, an aluminum coil rewinding machine needs to determine the predefined position of the wire. A predefined position is a measurement of the volume of the winding pack. This measurement can be achieved by measuring the fill factor.
The fill factor is determined by the volume of the winding pack. The volume of the winding pack depends on the number of windings in the pack. The fill factor is also a good indicator of how efficient a coil is. A densely packed pack of wires can be used to achieve a higher fill factor.
There are several winding technologies available for aluminum coil rewinding machines. The first is a linear winding technique. This method is most suitable for custom-made coils. The wire is fed through a guiding tube that is mechanically attached to the coil.
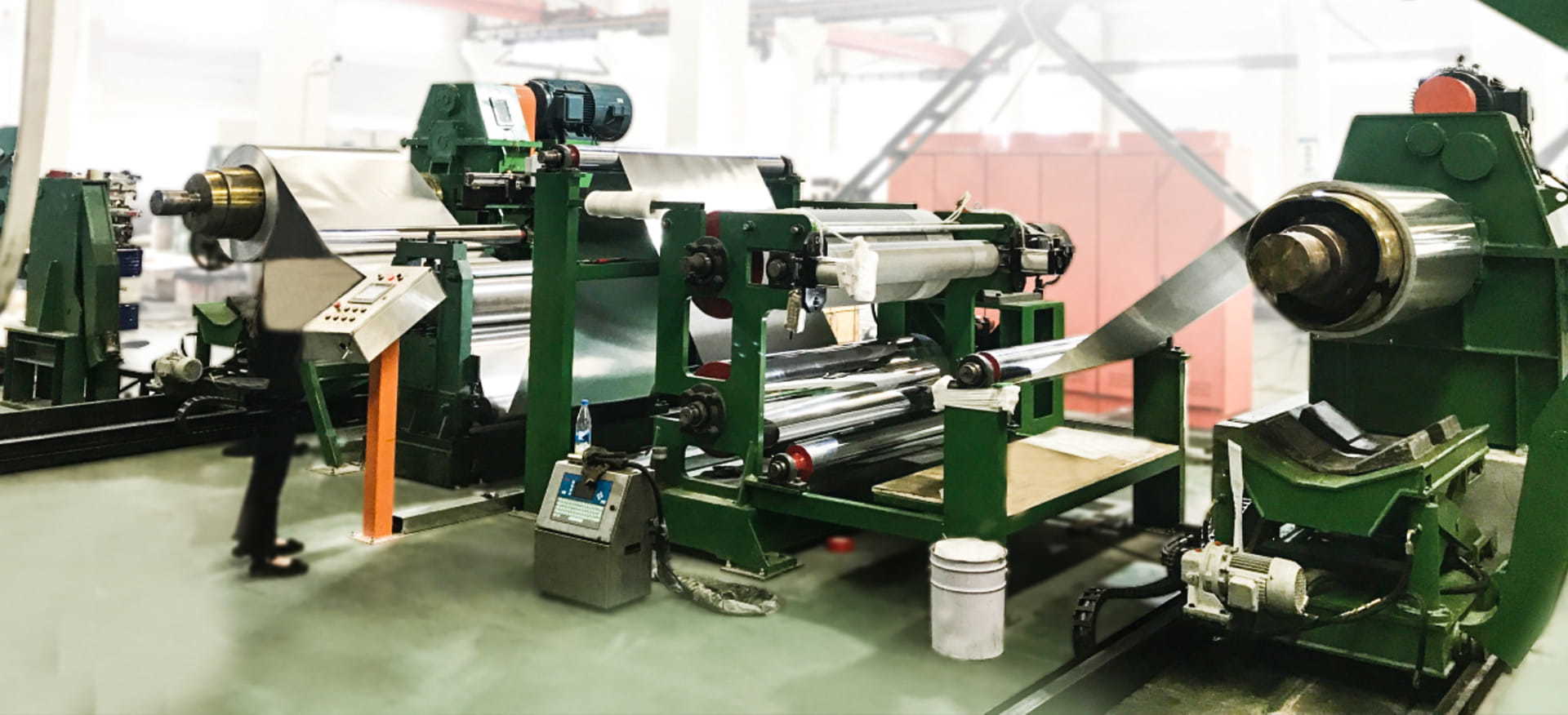
Several factors contribute to the maximum winding speed of aluminum coil rewinding machine. These factors include wire diameter, slot channel width, helix angle of angularly slotted stators, and needle stroke.
The maximum winding speed of aluminum coil rewinding machines is also influenced by the type of drive used. The drive can be a geared or a spindle drive.
The drive is used to generate a rotary motion which drives the wire. The wire is pulled from a supply roll of 400 kg copper wire. The wire is then coiled on a coil constructing appliance.
The wire is then fed through a guiding tube. The wire is then fed to a clamp device. The clamp device is used to hold the wire during the winding process.