The basic content and requirements of the light steel structure installation preparation work are the same as those of the ordinary steel structure installation project. During the construction of the steel column foundation, the positioning and protection of the anchor bolts should be done well, and the elevation of the top surface of the foundation and the anchor bolts should be controlled. After the foundation construction of the aluminum-plastic composite panel production line, the inspection and acceptance shall be carried out according to the following contents: 1) Whether the position of the axis of each row and column is correct; 2) Whether the span of each span meets the design requirements; 3) Whether the elevation of the top of the foundation meets the design requirements; 4) The feet Whether the position and elevation of the bolts meet the design and specification requirements. The mold used in the aluminum-plastic composite panel production line needs an upper mold and six lower molds of the same size. Install the upper mold and a lower mold first. The lower mold is directly installed on the hexagonal runner table, and the upper mold is installed on the bottom of the slide. and place a pad of appropriate thickness to ensure that after the upper and lower molds are closed, the gap between the four sides is uniform, and the distance between the upper and lower molds is equal to the required thickness of the tile. Then, the upper mold shall prevail, the worktable shall be indexed, and the remaining five lower molds shall be installed.
The aluminum-plastic composite panel production line manually places the blanks and takes the blanks. Before the equipment is used, it is necessary to check whether the connections are firm, whether the mounting bolts and nuts are tightened, and enough lubricating oil should be added to the left and right chassis before the machine can be powered on to start the machine for a test run. Carefully observe the empty car operation, whether there is vibration, noise, whether oil is coming from the oil window, whether the movement of each component is coordinated, and the mold can be installed after everything is normal. When installing the mold, the power must be cut off, and the motor belt or large gear must be moved manually Turn the worktable and make the slide seat rise to the highest point. It is best to use an object to support it between the worktable and the bottom surface of the slide seat, so that the anti-skid seat falls naturally and causes an accident.
In the operation process of the composite board production line, we must first select the panels, and clarify the type and type of materials and the commonality of colors. When selecting the panels, we should ensure that they are free of scars, warping, trachoma, depressions, stains, etc. If the board does not work, then it can be determined whether it can be used as a board after spraying the board with a water gun. In the pre-combination process of the panel, in case of a panel with a polished surface and a mesh, it should be selected and sent to a hand-held mill for fading, and dry grinding and leveling according to the flatness, but not deep grinding; then break off the mesh shovel plate If the surface glue cannot be removed by shovel, you should use a walking grinder to grind off the glue on the mesh surface to ensure the flatness of both sides and remove dust from the dry-grinded panel. In the pre-compounding process of the bottom plate of the composite board production line, the bottom plate with luminosity should be faded first and then the thickness should be determined. Generally, the thickness of the 20mm bottom plate should be set to 17mm. Remove moisture after the bottom plate is thickened. It can be pulled outside to dry, dry or blow dry. Pay attention to the fact that the board cannot be glued when it is not dry, to prevent delamination or lack of firmness. Glue and compound the composite board production line, check whether the panel and bottom plate of the composite board production line are dry, and pick out the board with moisture. Adjust the glue, mix the glue and calcium carbonate evenly, and adjust the toner to be basically the same as the color of the panel. According to the climate and humidity at that time, increase the curing agent in an appropriate amount, and the ratio of curing agent to glue is 1~3%. For compounding, first apply the adjusted glue separately and evenly on the composite surface of the panel and the bottom plate, then overlap the adhesive surface of the panel and the bottom plate, and then repeatedly push the center of the hand-pressing plate to let the air run out, and apply the same method. The second bottom plate, then attach the center clip and clamp it, and separate the small clips from the diagonal clips. After the four sides are clamped, check whether the clips are clamped one by one, and check whether the glue is evenly extruded on the four sides, otherwise it may be There is uneven gluing. Loosen the clip, the curing time is generally about 40 minutes before the clip can be loosened, otherwise it will be delaminated. After curing, loosen the clips of the composite panels in the composite panel production line and stack them in a regular manner, and record the manufacturing time, and wait for 5 to 8 hours before cutting.
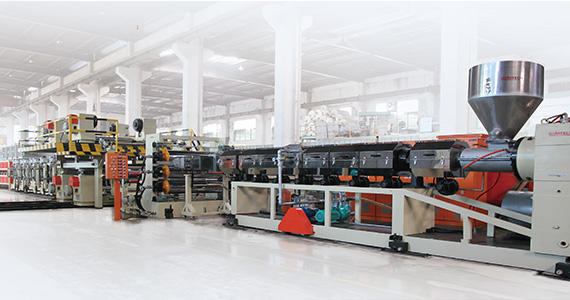