Sale Wholesale Aluminum Composite Panel Production Line Factory
In today's construction industry, Aluminum Composite Panel (ACP) has emerged as a versatile and popular material due to its lightweight nature, durability, and aesthetic appeal. ACP Production Line plays a crucial role in manufacturing these panels efficiently and ensuring their quality meets industry standards. This article delves into the key components and processes involved in ACP production, shedding light on the intricate mechanisms that drive this essential aspect of modern construction.
The ACP Production Line comprises several integral components, each contributing to the seamless manufacturing process. At its core, the line consists of a coil coating unit, where aluminum coils are coated with layers of paint or other finishes to enhance their appearance and protect against corrosion. These coated coils serve as the foundational material for ACP panels.
Next in line is the composite panel production unit, where the coated coils undergo a series of processes to form the final ACP product. This unit typically includes a coil unwinding machine, which feeds the coated coils into a continuous production line. The coils then pass through a series of rollers and presses, where they are shaped, bonded with a polyethylene core, and trimmed to the desired dimensions.
The bonding process is particularly critical in ACP production, as it ensures the structural integrity of the panels. High-pressure rollers apply uniform pressure to the composite materials, facilitating a strong bond between the aluminum layers and the core material. This step is carefully monitored to prevent defects such as delamination or uneven bonding, which can compromise the quality of the final product.
Once the panels are bonded, they undergo additional processes to enhance their appearance and performance. This may include surface treatments such as coating or laminating to provide additional protection against UV radiation, weathering, or fire. Quality control measures are implemented throughout these processes to detect any irregularities and ensure that the panels meet stringent industry standards.
Automation plays a significant role in modern ACP Production Lines, streamlining operations and improving efficiency. Advanced control systems monitor key parameters such as temperature, pressure, and coating thickness, allowing for precise adjustments to optimize production quality and minimize waste. Robotics and computerized machining equipment further enhance productivity by automating repetitive tasks and reducing human error.
Environmental sustainability is another key consideration in ACP production, with manufacturers increasingly adopting eco-friendly practices to minimize their carbon footprint. This includes recycling waste materials, optimizing energy usage, and reducing emissions throughout the production process. Additionally, the use of environmentally friendly coatings and core materials helps mitigate the environmental impact of ACP panels.
Looking ahead, the ACP Production Line industry is poised for continued growth and innovation. Advancements in materials science, automation technology, and sustainability initiatives are driving the evolution of ACP production, enabling manufacturers to produce higher-quality panels more efficiently than ever before. However, challenges such as fluctuating raw material costs, regulatory compliance, and market demand volatility remain constant concerns for industry stakeholders.
In conclusion, Understanding ACP Production Line: Key Components and Processes is essential for anyone involved in the construction industry. By gaining insight into the intricate workings of ACP production, stakeholders can make informed decisions to optimize efficiency, ensure product quality, and embrace sustainable practices. With continued innovation and collaboration, the ACP Production Line industry will continue to play a vital role in shaping the future of modern architecture and construction.
There are 15 days until Geartech participates in YAPI FUARI 2024. Welcome everyone to visit booth number H10 1103.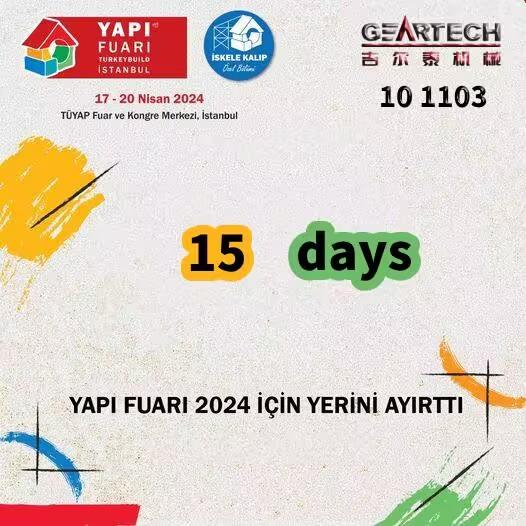