Sale Aluminum Composite Panel Production Coil Coating Lines
Aluminum composite panels (ACP) are widely used in modern construction, offering durability, aesthetic appeal, and versatility. As demand for these panels grows, manufacturers are under increasing pressure to improve efficiency while maintaining high-quality standards. The key to achieving this lies in optimizing the Aluminum Composite Panel Production Line, which serves as the backbone of the manufacturing process. In this article, we will explore strategies to streamline efficiency in the production line, reducing costs and increasing output without compromising on quality.
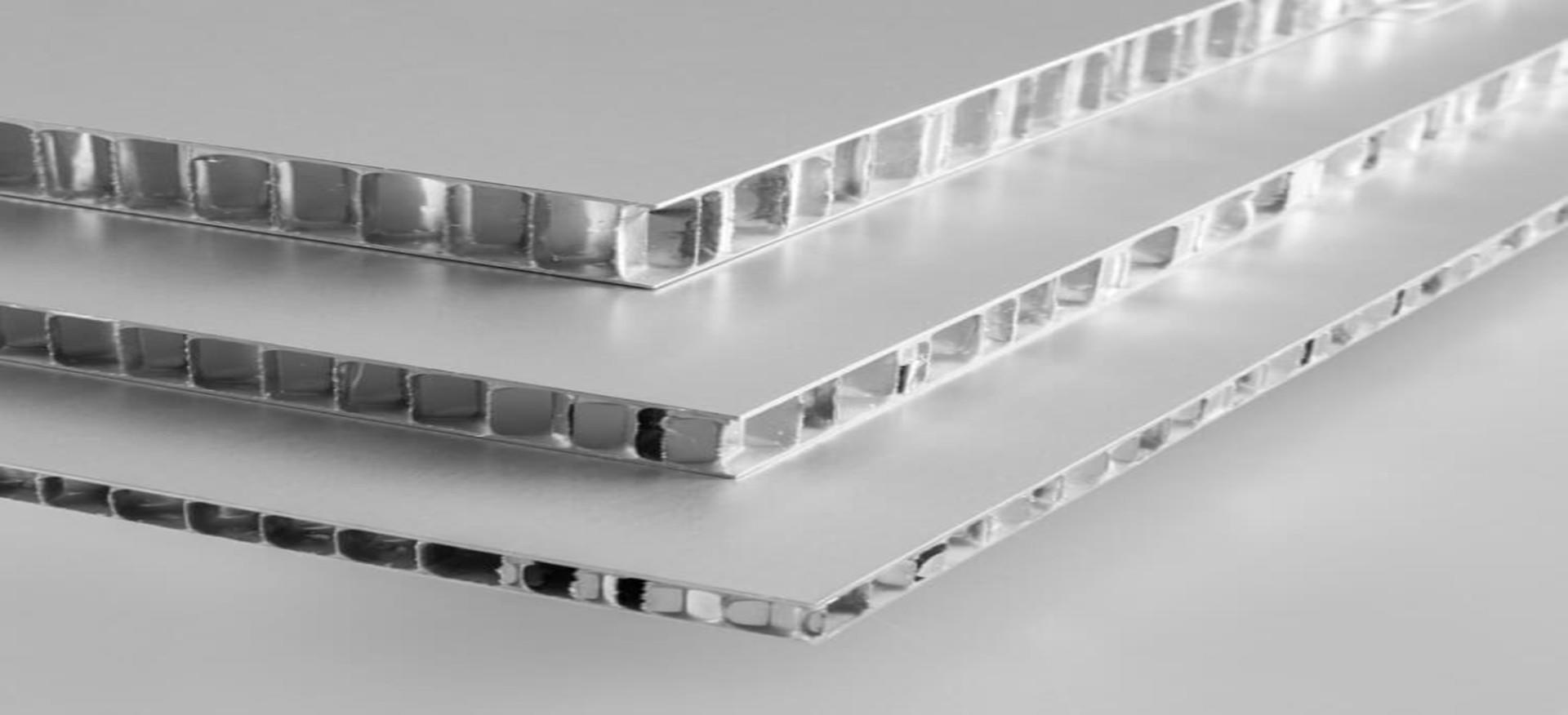
The Aluminum Composite Panel Production Line is a complex system that includes multiple stages such as material preparation, extrusion, coating, and assembly. Each of these stages involves various machines and processes that must work in harmony to produce a high-quality final product. By focusing on the entire production line, manufacturers can identify areas for improvement that advance to increased productivity and better overall performance.
1. Automation and Smart Technology Integration
One of the more effective ways to streamline the Aluminum Composite Panel Production Line is by incorporating automation and smart technology. Automation helps reduce human error and speeds up repetitive tasks, which can significantly boost productivity. For example, automated cutting and stacking systems can handle large volumes of material more quickly and with greater precision than manual labor. Furthermore, integrating sensors and IoT (Internet of Things) technologies into the production line enables real-time monitoring, providing manufacturers with immediate feedback on machine performance, material usage, and potential bottlenecks.
By using smart technology, manufacturers can predict maintenance needs before breakdowns occur, thereby reducing downtime. Predictive maintenance tools can monitor the health of machines along the Aluminum Composite Panel Production Line and schedule repairs only when necessary, rather than relying on fixed maintenance intervals. This proactive approach not only extends the lifespan of the equipment but also improves overall efficiency.
2. Material Selection and Waste Reduction
Reducing waste is a critical aspect of streamlining any production line. In the case of the Aluminum Composite Panel Production Line, careful selection of raw materials and efficient use of resources can contribute significantly to cost savings. ACPs consist of an aluminum skin and a non-aluminum core, and ensuring that these materials are of high quality and consistent thickness can improve yield rates.
To reduce waste, manufacturers can implement advanced cutting techniques and optimize material handling systems. For example, nesting software can be used to calculate the more efficient way to cut panels, ensuring small scrap material. This reduces the overall cost of raw materials while also improving production speed, as fewer interruptions occur due to material shortages or waste disposal.
3. Standardization and Process Control
Consistency across all stages of the Aluminum Composite Panel Production Line is essential for achieving high-quality results. One of the more effective ways to ensure this is through standardization. By implementing standard operating procedures (SOPs) and rigid process controls, manufacturers can reduce variability in their production processes.
For example, temperature and pressure control during the coating and bonding stages of ACP production are critical for ensuring a strong bond between the aluminum skin and the core material. By installing advanced control systems that maintain consistent environmental conditions, manufacturers can reduce the chances of defects such as delamination or inconsistent finishes. This level of precision also helps to streamline the production process, as fewer products will need to be reworked or discarded.
4. Lean Manufacturing Techniques
Lean manufacturing techniques have long been used to improve efficiency in production lines across various industries. By applying principles such as continuous improvement, waste reduction, and value stream mapping, manufacturers can identify areas within the Aluminum Composite Panel Production Line that may benefit from process improvements.
For example, reducing the time spent on setup and changeovers can advance to greater flexibility and faster response times to customer demands. In a fast-paced manufacturing environment, less downtime between production runs can significantly increase the throughput of the Aluminum Composite Panel Production Line. Implementing just-in-time inventory management techniques can also help reduce excess stock and the associated storage costs, allowing for smoother and more efficient production schedules.
5. Employee Training and Involvement
While automation and technology play crucial roles in streamlining efficiency, human expertise is still essential to the success of the Aluminum Composite Panel Production Line. Investing in employee training is key to ensuring that the workforce is equipped to handle the latest machines and technologies effectively.
Cross-training employees across multiple stages of the production process allows for greater flexibility and better problem-solving. Employees who understand the entire flow of the Aluminum Composite Panel Production Line are better able to identify inefficiencies, troubleshoot problems, and suggest improvements. Moreover, fostering a culture of continuous improvement can motivate employees to take ownership of their work, and pilot more proactive efforts in maintaining high-efficiency levels throughout the production cycle.
Streamlining the Aluminum Composite Panel Production Line is essential for maintaining competitiveness in a growing market. By embracing automation, improving material handling, and incorporating lean manufacturing principles, manufacturers can boost efficiency while ensuring high-quality output. Standardization and process control will further help reduce variability, and investing in employee training can create a more responsive and skilled workforce. In an ever-evolving industry, these strategies will allow manufacturers to meet customer demands, reduce costs, and position themselves for long-term success in the aluminum composite panel market.