High Quality Aluminum Composite Panel Production Coil Coating Lines
The aluminum composite panel production line plays a crucial role in the manufacturing of durable and aesthetically appealing building materials. These panels are widely used in exterior and interior facades, signage, and cladding due to their combination of lightweight properties, strength, and ease of maintenance. To achieve these benefits, the production process must be carried out with precision and attention to detail. In this article, we will explore the key components that make up the aluminum composite panel production line and the role they play in ensuring a smooth and efficient manufacturing process.
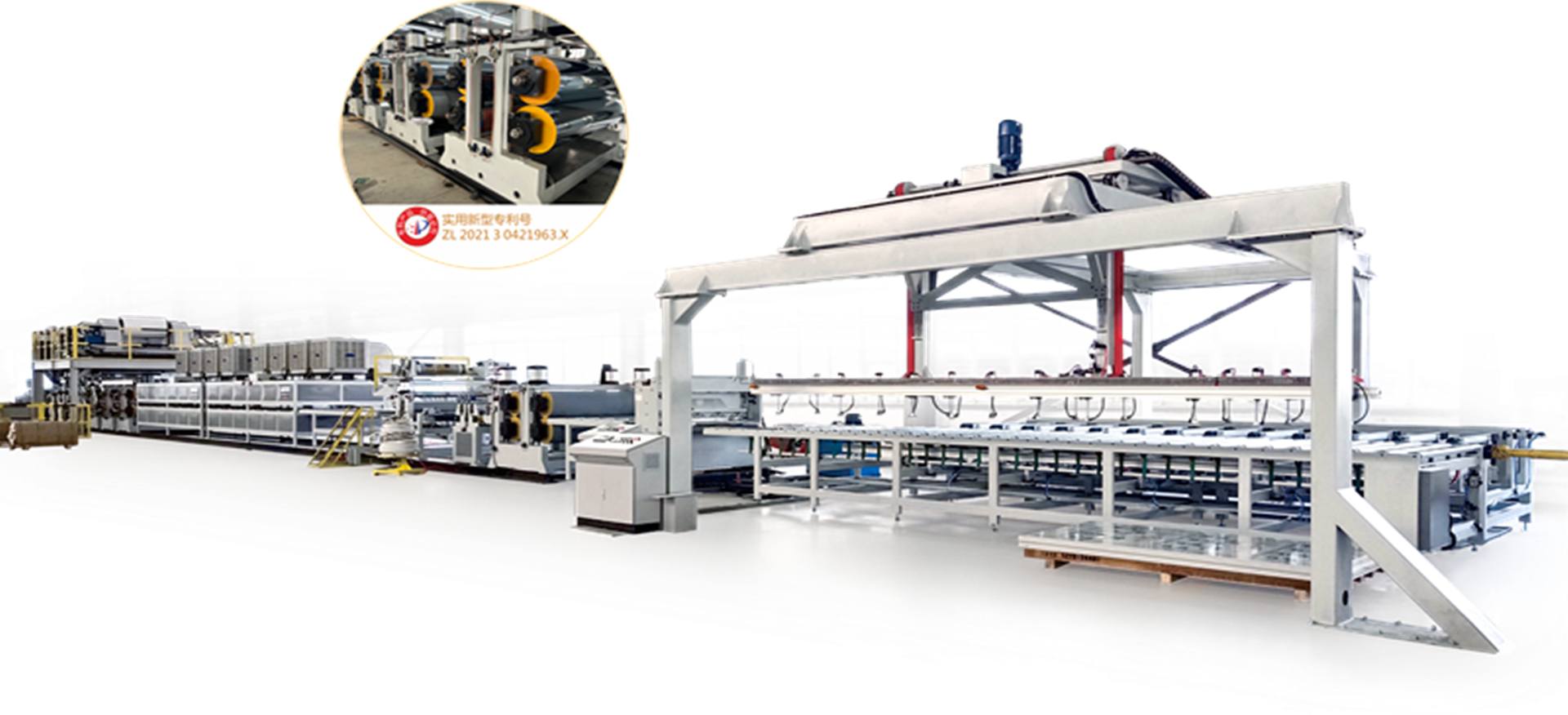
The Aluminum Composite Panel Production Line consists of several stages, each involving specialized machinery and technology to process raw materials into finished panels. These stages include the preparation of materials, assembly, coating, pressing, cutting, and packaging. Understanding these steps is essential for manufacturers aiming to optimize their operations and ensure product quality.
The one key component of an aluminum composite panel production line is the preparation of raw materials. Aluminum coils, the primary material used in the production of these panels, must be sourced and prepared for processing. The aluminum coils are often coated with a protective layer to prevent corrosion and ensure durability. In this stage, the coils are unrolled and cleaned to remove any contaminants. The cleaning process is critical, as any dirt or grease can negatively impact the quality of the final product.
Once the raw materials are prepared, the next crucial step in the Aluminum Composite Panel Production Line is the assembly of the core material. The aluminum sheets are bonded together with a non-aluminum core, typically made of polyethylene or mineral-based material. This core provides the panel with its lightweight properties while maintaining the rigidity required for various applications. The core material is precisely applied to the inner layer of aluminum sheets, ensuring that the panel's strength and performance meet the required standards.
The coating process is another essential component of the Aluminum Composite Panel Production Line. The aluminum sheets are coated with a layer of paint or other materials to enhance both their appearance and weather resistance. The coating is typically applied using roller or spray coating techniques, ensuring a uniform finish. This step not only improves the aesthetic value of the panel but also helps extend its lifespan by protecting it from environmental elements such as UV radiation and moisture.
After the coating process, the panels move to the pressing stage. In this stage, the aluminum sheets are bonded with the core material using a high-pressure laminating machine. This process ensures that the panel maintains its strength and durability while also achieving a smooth, even surface. The pressure applied during the pressing stage helps to eliminate any air pockets or imitations that could affect the panel's overall quality. The Aluminum Composite Panel Production Line uses advanced technology to control the temperature and pressure during pressing, guaranteeing that the finished panels meet stringent quality standards.
The cutting process follows pressing, where the panels are cut to the desired size and shape. Cutting is a critical component of the Aluminum Composite Panel Production Line because it ensures that the panels meet the specifications required for different applications. Panels may need to be cut into various sizes, such as standard sheets or custom-sized pieces, depending on the end-use. The cutting machines used in this stage are equipped with high-precision tools to ensure clean, accurate cuts that less waste.
After the panels are cut to size, they undergo a final inspection to ensure that they meet all quality requirements. Any panels that do not meet the necessary standards are removed from the production line to avoid any defects being passed on to customers. This quality control stage is essential for maintaining the integrity of the Aluminum Composite Panel Production Line and ensuring that only the ideal products reach the market.
Finally, the panels are packaged and prepared for shipping. The packaging process involves carefully wrapping the panels to protect them from damage during transport. Protective materials, such as plastic film or foam padding, are often used to prevent scratches or dents from occurring. Once the panels are securely packaged, they are ready to be sent to customers for use in construction, signage, or other applications.
Throughout the entire process, automation plays a key role in ensuring the efficiency and accuracy of the Aluminum Composite Panel Production Line. Modern production lines use advanced control systems to monitor each stage of the process, from raw material preparation to final inspection. These systems help reduce human error, improve production speed, and ensure that the panels meet quality standards consistently.
In conclusion, the Aluminum Composite Panel Production Line is a highly specialized manufacturing system that involves various stages of processing, from raw material preparation to the final packaging of the panels. Each component of the production line, including material preparation, assembly, coating, pressing, cutting, and packaging, plays a critical role in ensuring the production of high-quality aluminum composite panels. As demand for these panels continues to grow, manufacturers must focus on optimizing their production lines to maintain efficiency, reduce waste, and produce panels that meet the needs of the construction industry and other sectors.