Sale ACP Production Line Aluminum Laminate Panel Factory Manufacturer
The ACP Production Line has become a critical component in the manufacturing of aluminum composite panels, a material widely used in construction and architectural designs. As industries continuously evolve, there is an increasing need to improve the efficiency and effectiveness of the ACP Production Line. Streamlining manufacturing processes not only reduces costs but also enhances the overall quality of the final product, enabling manufacturers to meet growing demand and expectations.
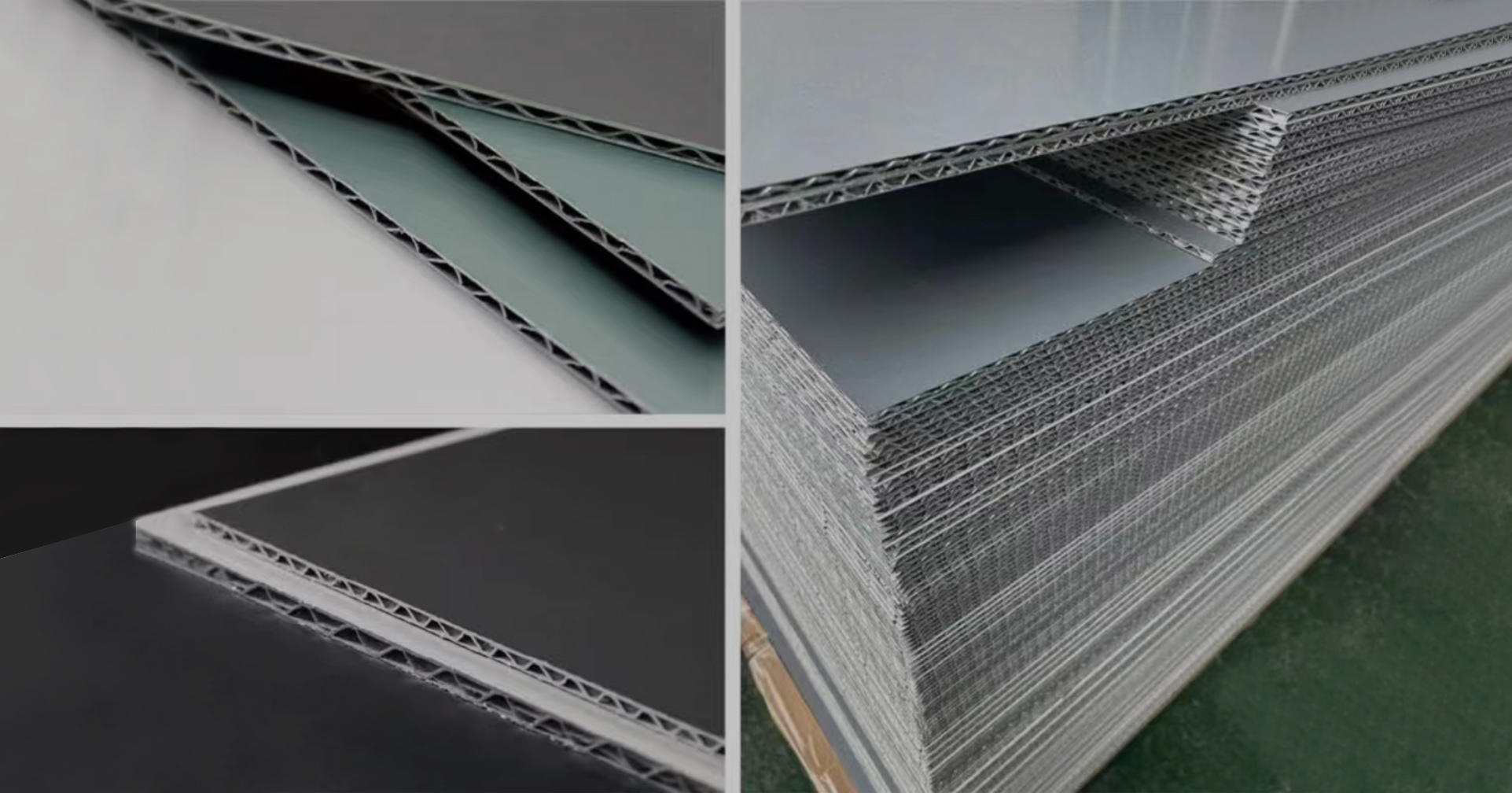
One of the core aspects of the ACP Production Line is automation. By integrating advanced machinery and robotics, manufacturers can significantly reduce human error, increase speed, and improve precision. The automation of various stages within the ACP Production Line, from material handling to assembly, has proven to be highly effective in boosting overall productivity. Additionally, automation allows for continuous operation, making it possible for production to run 24/7 with small downtime, which is critical in meeting large-scale orders.
Another important factor in streamlining the ACP Production Line is the improvement in raw material handling. In traditional setups, the handling and processing of aluminum sheets and other materials were time-consuming and piloted to inefficiencies. However, modernized ACP Production Lines employ automated systems to move raw materials seamlessly through the different stages of production. This not only speeds up the process but also ensures that materials are handled with care, reducing the risk of damage or waste. With more efficient material management, manufacturers can achieve a higher throughput while reducing the costs associated with waste and reprocessing.
In addition to material handling, energy efficiency plays a significant role in optimizing the ACP Production Line. By utilizing energy-efficient machines and systems, manufacturers can lower their operational costs. For example, newer models of heat exchangers and power units are designed to reduce energy consumption without compromising the quality of the panels produced. The ACP Production Line can benefit from energy-efficient technology in both the production process and the machinery used, ultimately piloting a reduction in the carbon footprint of the manufacturing process.
The integration of advanced software also contributes to the efficiency of the ACP Production Line. Manufacturing execution systems (MES) are used to monitor and control every aspect of the production process. From tracking materials and production progress to ensuring product quality, MES enables manufacturers to optimize the workflow in real time. This digital integration helps in identifying bottlenecks, fewer delays, and improving overall communication between different stages of the production line. Through continuous monitoring, manufacturers can detect potential issues early and make adjustments to keep the ACP Production Line running smoothly.
The ACP Production Line also benefits from the constant innovation in materials used during the production process. Research and development in the field of aluminum composite materials have led to the creation of lighter, more durable, and more sustainable panels. These innovations allow manufacturers to produce high-quality products more efficiently. By selecting the right materials that can withstand harsh environmental conditions, manufacturers can ensure that the final product has a longer lifespan and meets the standards required by their customers.
Quality control is an area that has seen significant improvements in the ACP Production Line as well. With the use of precision sensors and automated testing systems, manufacturers can ensure that every panel produced meets the required specifications. These systems can quickly detect any discrepancies in the panels, such as surface defects or thickness variations, ensuring that only the high-quality products leave the production line. Enhanced quality control advances to fewer returns and reworks, saving both time and money.
Finally, the ACP Production Line's ability to adapt to different production volumes is a key factor in maintaining efficiency. Modernized systems are designed to handle both small and large-scale orders without compromising speed or quality. This flexibility allows manufacturers to respond quickly to customer demands, whether it's for a bulk order or a custom project. The scalability of the ACP Production Line ensures that manufacturers can stay competitive in an ever-changing market.
In conclusion, the ongoing innovations in the ACP Production Line are transforming the way aluminum composite panels are manufactured. By focusing on automation, energy efficiency, material handling, and quality control, manufacturers can streamline their processes and increase productivity. As these technological advancements continue to evolve, the ACP Production Line will only become more efficient, ensuring that the demand for aluminum composite panels can be met without compromising on quality or cost.